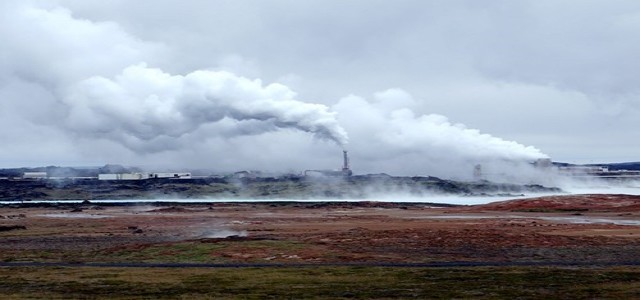
Armstrong International, a leading provider of thermal energy solutions, has reportedly partnered with Everactive, a breakthrough battery-less IoT company. Through this alliance, Everactive will integrate its real-time monitoring tech with SAGE®, Armstrong International’s software for steam trap management.
The collaboration will offer a world-class solution for curbing steam losses and minimizing excess CO2 emissions and associated energy costs. This partnership exhibits the power of smart technology to substantially impact the industrial sector, as it keeps on modernizing and offering efficiencies across all industries.
Battery-less sensors provide the most affordable method of monitoring at scale, offering always-on, reliable, and maintenance-free wireless technology. The steam trap management of Armstrong provides deep knowledge as well as resources to further advance valuable steam systems that are at the center of petrochemical refining, process manufacturing, along with district energy operations.
John Greenfield, the Vice President of Partnerships at Everactive, expressed that the integration of the company’s steam trap monitoring system into SAGE® software represents an impressive combination of industrial domain expertise and new technology, that stands to generate immense savings for their joint consumers.
He added that including real-time, scalable monitoring to the trap management tool suite of Armstrong will help a range of industries in achieving their goals of cost-savings, decarbonization, and energy reduction.
The ultra-low-power semiconductors of Everactive need a thousand times less power than other competing circuits. The company’s sensor devices can generate sufficient power from pockets of harvested energy to continuously process, measure, and wirelessly transmit data of equipment and infrastructure health from a wide range of industrial assets, which includes steam traps.
By recognizing and reacting to active trap failures, the integrated solution enables consumers to reduce steam loss and thus curb energy costs and surplus CO2 emissions related to wasted steam. For a single facility, this can be calculated in thousands of tons of carbon dioxide and millions of dollars, which results in optimizing reliability and efficiency whilst minimizing the footprint of the IT infrastructure.
Source credits: